Overview
The DRP (Distribution Requirements Planning) module is an Inventory Planning tool that supports the planned replenishment of Items within a Division, Project, Site and Location either via Purchase transactions or Site/Location transfers. Inventory levels are managed by setting Minimum Stocking Quantity and Desired Holdings within the DRP Location Replenishment Maintenance module and Inventory Requisitions or Planned Transfers created by running the DRP Processing routine.
Click on the image to enlarge. It contains hyperlinks to related articles.
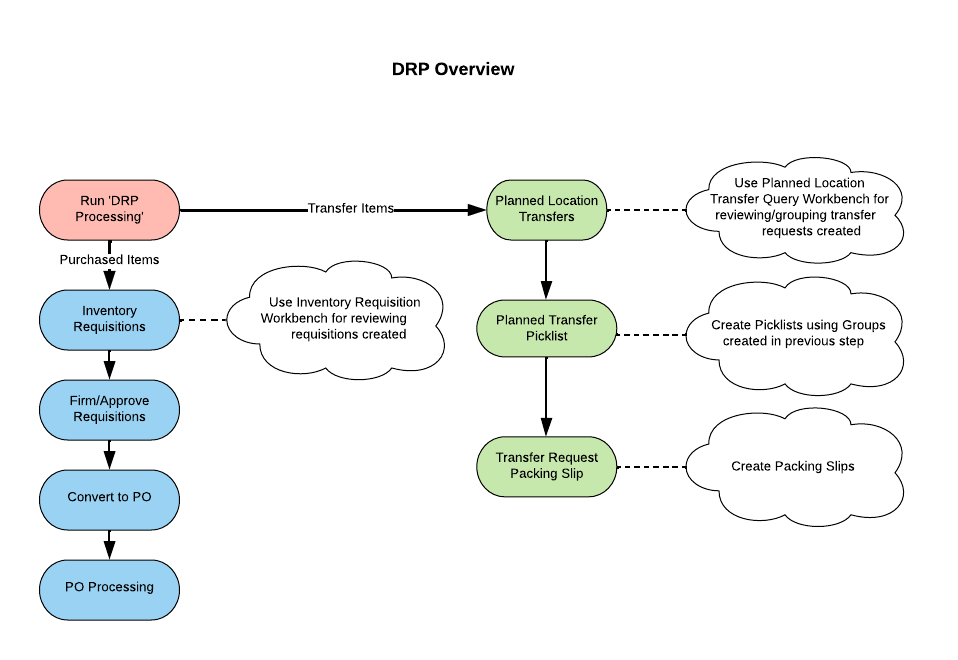
Application
DRP function is a tool to manage, within a specific Division, the desired levels of inventory of an item at a Division/Site/Location ID/Location No.
The user-entered settings for an item on its DRP Location Replenishment Maintenance record define the policy for that item in the Division/Site/Location ID/Location No.
When the user runs the DRP processing function and replenishment is required based on the user-defined policy for the item in a Division/Site/Location ID/Location No, either:
-
A planned location transfer is created,
-
An Inventory Requisition was created.
NOTE When appropriate, manual Planned Location Transfer records can be entered.
DRP Location Replenishment Maintenance records flagged as Create Purchase Requisition will produce an Inventory Requisition that can be reviewed and converted into a Purchase Order (via the Inventory Requisition Workbench) to manage the replenishment of the Site/Location. Site to Site or Location to Location Transfers can be achieved by setting the From and To Site/Locations accordingly and DRP will produce a Planned Location Transfer that can be grouped into a consolidated Planned Transfer Pick and Packing Slip via the Planned Location Transfer Query module.
DRP is enabled by configuring and utilizing the following functions:
Navigation
DRP Processing
-
DRP Location Replenishment Maintenance: Create DRP Location Replenishment Maintenance records (Purchased or Transfer).
-
DRP Processing: The tool used to launch DRP Processing. There are two modes available:
-
Full Regeneration: This mode will process all DRP Replenishment records. Any Planned Inventory Requisitions or Transfers (not Firmed) will be deleted and regenerated.
-
MRP/DRP Net Change: Refer to the Net Change document for more information.
-
Planned Transfer Picklist: Tool used to create Picklists for Planned Transfer requests.
-
Planned Location Transfer Maintenance: Any DRP Location Replenishment Maintenance records configured as Transfers will create records that appear in the Planned Location Transfer Maintenance module for review/amendments.
-
Planned Location Transfer Query: Tool used to manage Transfer requests in bulk and Group into a single Picklist.
-
Inventory Requisition Workbench: Any DRP Location Replenishment Maintenance records flagged as Purchased Items will appear in the Inventory Requisition Workbench in readiness for conversion to PO's.
-
Transfer Request Packing Slip: Tool used to create Packing Slips for Planned Transfer Requests.
Table of Contents
DRP Location Replenishment Maintenance
DRP Processing
Planned Location Transfer Maintenance
Planned Location Transfer Query
Planned Transfer Picklist
Transfer Request Packing Slip
Scheduled DRP
DRP Log
MRP / DRP Net Change