Overview
DRP Processing launches the creation of Planned Location Transfers and Inventory Requisitions in accordance with the records created in the DRP Location Replenishment Maintenance module.
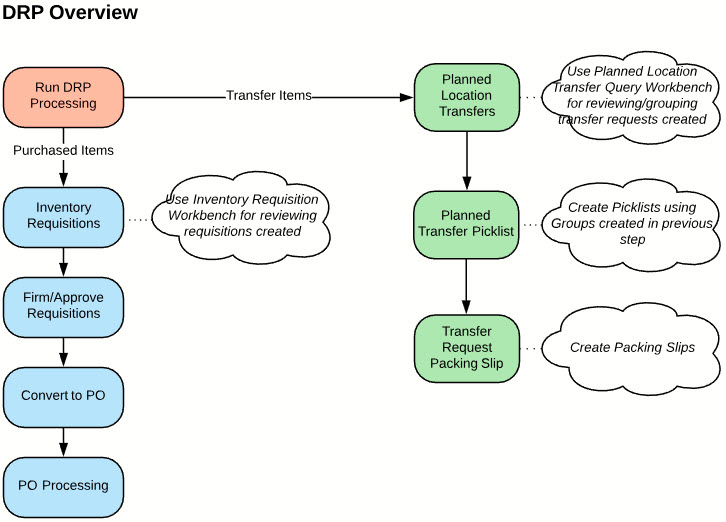
Application
DRP Processing when run regularly will ensure replenishment transactions are created to maintain Inventory levels as defined in the DRP Location Replenishment Maintenance parameters. DRP can be run manually or as a Scheduled DRP job. There are two modes that can be used:
- Full Regeneration: Processes all Replenishment Location Maintenance records. Any Planned Transfers or Inventory Requisitions that are not Firmed will be deleted and recreated in the process (if applicable). This mode takes longer to process as it assesses each replenishment record.
- Net Change: Net Change mode will only process Items where there have been changes (changes to Inventory Levels/Requisitions etc) since the last DRP run and therefore require re-planning for the item. When the Net Change DRP option is used, when changes occur to the Item or Item hierarchy, the new Item / Commodity Code flags for Net Change get set to True based on several events. Refer to the MRP/DRP Net Change article for more information.
IMPORTANT The DRP routine can be referencing large amounts of data within the Org. Processing time is increased based on the number of DRP Location Replenishment Maintenance records created. It is suggested to run DRP outside of normal operating hours to reduce latency that may be experienced whilst the routine is processing.
The DRP process evaluates items based on their configuration in the Inventory Item Master. The following considerations apply:
- Associated Items without DRP Equivalents: For items that do not have Associated Items (Relationship = DRP Equivalent) defined, the DRP process calculates quantity directly based on the DRP Location Replenishment record.
- Associated Items with DRP Equivalents: When Associated Items (Relationship = DRP Equivalent) are defined on the Inventory Item Master, the DRP process includes these equivalents in its calculations.
-
- The system accounts for these equivalents to ensure optimal planning.
- Corresponding PLT records are generated to reflect the consideration of DRP Equivalents.
Examples:
Scenario 1: The Inventory Item Master has no associated items defined as DRP Equivalents.
- Battery A has no associated items defined.
- Current Inventory in Site/Location ID/Location Number is 10
- A DRP Location Replenishment record is created for a desired quantity of 25
- Run the DRP process
- Once the process is completed successfully, the system will create a Planned Location Transfer Request for 15.
Scenario 2: The Inventory Item Master has an associated item that is defined as DRP Equivalents
- Battery A has one associated item Battery B defined as a DRP Equivalent.
- Current Inventory in Site/Location ID/Location Number is 10 for Battery A and 20 for Battery B
- A DRP Location Replenishment record is created for a desired quantity of 25 for Battery A
- Run the DRP process
- Once the process is completed successfully, the system will not create any Planned Location Transfer records as the combined inventory of Battery A and Battery B will meet the required need.
Scenario 3: The Inventory Item Master has an associated item that is defined as DRP Equivalent
- Battery A has one associated item Battery B defined as a DRP Equivalent.
- Current Inventory in Site/Location ID/Location Number is 10 for Battery A and 20 for Battery B
- A DRP Location Replenishment record is created for a desired quantity of 50 for Battery A
- Run the DRP process
- Once the process is completed successfully, the system will create a Planned Location Transfer record for a quantity of 20. This is because the combination of inventory for Battery A and Battery B is 30, so the system will create a planned location transfer for the remaining quantity, which is 20 in this example.
This approach ensures planning aligns with item relationships configured in the Inventory Item Master.
Prerequisites
Terminology
DRP: Distribution Requirements Planning
Planned Location Transfer: A DRP generated or manual entry Planned Location Transfer record that facilitates the transfer of Inventory from one Location to another.
Purchase Requisition: A DRP generated Inventory Requisition that can be converted into a Supplier Purchase Order.
Navigation
DRP Processing
Processing
User Initiated Processing:
- Confirm the correct Division is assigned
- Set DRP Processing Mode as required (Net Change or Full Regeneration)
- Click Start Process
Scheduled DRP: Refer to the Scheduled DRP article for setup instructions.
Once the DRP Processing routine is complete, Purchase Requisitions and Planned Location Transfers will be created in accordance with the DRP Location Replenishment Maintenance records. Purchase Requisitions can be reviewed in the Inventory Requisition Workbench function. Planned Location Transfers can be reviewed in the Planned Location Transfer Query function.
SEE ALSO
DRP Location Replenishment Maintenance
Planned Transfer Picklist
Planned Location Transfer Maintenance
Planned Location Transfer Query
Inventory Requisitions
Inventory Requisition Workbench
DRP Log