Overview
Rootstock ERP provides two Inventory Valuation methods, Standard Cost and Weighted Average. This article details how Standard Costs are maintained and used throughout the system.
Application
The steps below are to be followed when the standards are to be updated or when initializing an org, in which case it is a good practice to add Inventory to the system after Standard Costs have been established.
Click on the image to enlarge. It contains hyperlinks to related articles.
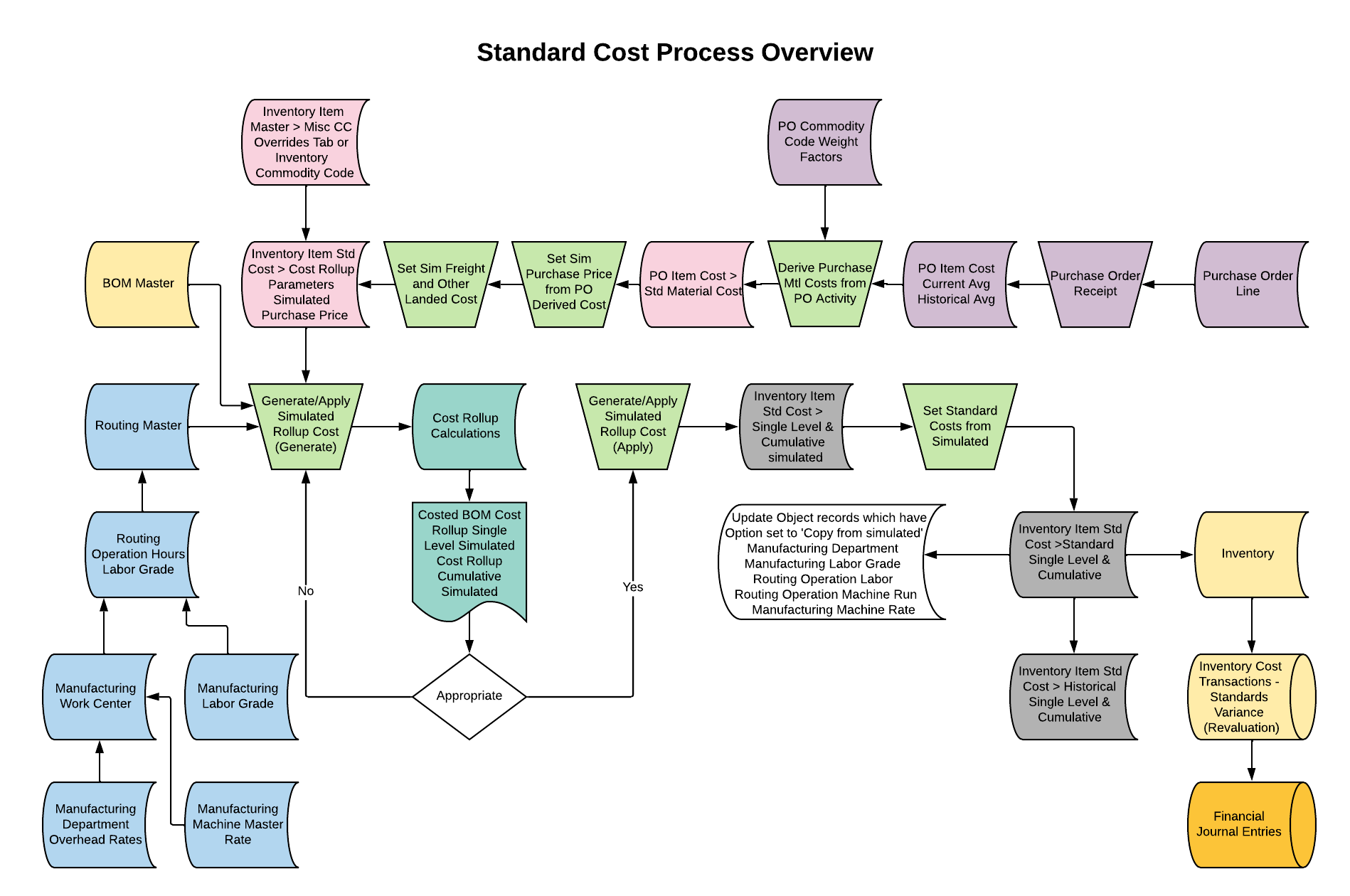
Standard Cost Setup
1. Purchased Material Cost
Navigation > Purchase Item Cost
The PO Item Cost record contains the calculated Current and Historical Average Price paid for an item. These values are calculated from Purchase Order Receipts. The Std Material Cost is calculated by multiplying the Current and Historical Average Price from the PO Item Cost record times the Current and Historical Weight Factors and the Std Cost Markup/Down in the Purchase Order Commodity Code record.
This record also has a control indicator, Std Cost Update Ind which when set to Calculate and the Set Sim Purchase Price From PO Derived Cost function is selected, will populate the Inventory Item Std Cost > Simulated Purchase Price cost. In a Simulated Rollup Cost, the item's Simulated Purchase Price is multiplied by the bill of material component quantity to calculate the simulated material cost.
Navigation > Purchase Order Commodity Code
The record holds the Current and Historical Weight Factor and the Std Cost Markup/Down values that are used in the calculation of the Std Material Cost on the PO Item Cost record.
2. Material Overhead Rate
Navigation > Inventory Commodity Code > Accounting Tab
It contains the Material Overhead Rate value that is multiplied times the cost of Inventory Item Std Cost > Simulated Purchase Price to calculate a Material Overhead cost. This value can be overridden on the Inventory Item Master record.
3. Labor Overhead Rates
Navigation > Manufacturing Department
The overhead rates used in the calculation of labor and fringe overhead values are assigned in the Manufacturing Department record.
-
Labor Overhead: The Simulated Labor Overhead Rate value is the rate used in the Simulated Rollup Cost calculation. The Simulated Labor value (the operation Simulated Hourly Rate multiplied by the Simulated Run Hours and Simulated Setup Hours) is multiplied by the Simulated Labor Overhead Rate to calculate the labor overhead cost. The Standard Labor Overhead Rate value is the Simulated Labor Overhead Rate in effect when the current standard cost was set.
-
Fringe Overhead: The Simulated Fringe Overhead Rate value is the rate used in the Simulated Rollup Cost calculation. The Simulated Labor value (the operation Simulated Hourly Rate multiplied by the Simulated Run Hours and Simulated Setup Hours)is multiplied by the Simulated Fringe Overhead Rate to calculate the fringe overhead cost. The Standard Fringe Overhead Rate value is the Simulated Fringe Overhead Rate in effect when the current standard cost was set.
4. Labor Rate
Navigation > Manufacturing Labor Grades
The Manufacturing Labor Grade is entered on the routing operation. The Manufacturing Labor Grade assigned to the routing operation is multiplied by the routing operation time.
The Simulated Hourly Rate value is the rate used in the Simulated Rollup Cost calculation. In a Simulated Rollup Cost, the Simulated Hourly Rate is multiplied by the Routing Operation Simulated Run Hours and Operation Simulated Setup Hours to calculate labor cost. The Standard Hourly Rate value is the Simulated Hourly Rate in effect when the current standard cost was set.
5. Machine Overhead Rates
Navigation > Manufacturing Machine Master
This record contains the overhead rate for the machine. When a Manufacturing Machine Master is assigned to a Routing operation the reported time is multiplied by the rate.
The Simulated Hourly Rate value is the rate used in the Simulated Rollup Cost calculation. In a Simulated Rollup Cost, the Simulated Hourly is multiplied by the Routing Simulated Operation Machine Hours to calculate machine cost. The Standard Hourly Rate value is the Simulated Hourly Rate in effect when the current standard cost was set.
6. Routing Labor Times and Setup Times
Navigation > Routing Operations
The routing operation has two places to enter hours (operation time). One is a Run Hours and the other is Setup Hours.
-
Run Hours (Labor): The Run Hours are entered on the Routing Operation. In a Simulated Rollup Cost, the Simulated Hourly Rate of the assigned Labor Grade is multiplied by the routing operation Simulated Run Hours to calculate a Simulated Labor Cost. The operation Standard Run Hours value is the Simulated Run Hours in effect when the current standard cost was set.
-
Setup Hours: The Setup Run hours are entered on the Routing Operation. In a Simulated Rollup Cost, the Simulated Hourly Rate of the assigned Labor Grade value is multiplied by the Simulated Setup Hours to calculate a Simulated Labor Cost. The operation Standard Setup Hours value is the Simulated Setup Hours in effect when the current standard cost was set.
7. Machine Times
Navigation > Routing Operations
When a machine master is assigned to an operation the machine hours are entered on the Routing Operation. In a Simulated Rollup Cost, the Machine Simulated Hourly Rate is multiplied by the routing Simulated Machine Hours calculate a Simulated Machine Cost. The Standard Machine Hours are the Simulated Machine Hours used in the Simulated Rollup Cost calculation from which the current standard cost was set.
When Freight and Landed Costs are used in a Standard Cost Division
8. Freight
When Freight is used in a Standard Cost Division, the value of the item's freight cost is manually entered to the Inventory Item Standard Cost Cumulative Simulated Freight cost field after the Apply Simulated Rollup Cost is run and prior to Set Standard Costs from Simulated is run.
9. Standard Other Landed
When landed cost is used in a Standard Cost Division, the value of an item's landed cost is manually entered to the Inventory Item Standard Cost Cumulative Simulated Freight cost field after the Apply Simulated Rollup Cost is run and prior to Set Standard Costs from Simulated is run.
10. Bill of Material
Navigation > Engineering BOM Master
The Bill of Material contains the component items used in the manufacture of the parent item. This is the structure used in the Generate Simulated Rollup Cost function. The quantity per of the item in the Bill of Material is multiplied by the Inventory Item Standard Cost Simulated Purchase Price of the item.
11. Inventory Item Standard Cost record
Navigation > Inventory Item Standard Costs
This record contains an item's Cumulative and Single Level Standard cost, Cumulative and Single Level Simulated cost, and Cumulative and Single Level Historical Cost. In addition, it contains cost update settings. This record is the source of the standard cost of the item in a standard cost division.
Standard Costs - Calculation & Processing steps
Steps to derive Purchase Price from Purchase activity into Simulated Rollup Costs:
1. Navigation > Purchase Item Cost
-
A record is created by the software for each purchased Item. The record contains a current quantity received, a current amount received, and a calculated current average cost. The current values are derived from the Purchase Order item receipt transactions. The record also has fields containing the historical values of the received quantity and amount and an average cost.
2. Navigation > Derive Purchase Mtl Costs from PO Activity
NOTE When the PO Item Cost > Std Cost Update Ind is set to 'Manual' the user must manually populate the PO Item Cost > Std Material Cost value.
3. Navigation > Set Sim Purchase Price From PO Derived Costs
-
When this option is selected, and the PO Item Cost > Std Cost Update Ind is set to 'Calculate', the PO Item Cost > Std Material Cost value is populated to the Inventory Item Std Cost > Cost Rollup Parameters > Simulated Purchase Price. If the PO Item Cost > Std Cost Update Ind is set to 'Manual' the user must manually enter a value in the Inventory Item Std Cost > Cost Rollup Parameters >Simulated Purchase Price.
NOTE For a purchased item, the cost in the Simulated Purchase Price field is the material cost used when the Generate/Apply Simulated Rollup Costs 'Generate' option is selected.
4. Navigation > Set Sim Freight and Other Landed Cost
-
-
- This function ensures the accurate simulation of Freight and Other Landed costs for PO receipts processed with FLC charges. Additionally, it updates the Inventory Item Cost value to reflect these charges accurately.
NOTE This opens the VisualForce classic page Auto Set Item Standard Freight Othlnd Cost.
Steps to calculate and apply Simulated costs into Standard:
1. Navigation > Generate-Apply Simulated Rollup Costs
When the 'Generate' indicator is selected, a Simulated Rollup Cost is performed by populating the Cost Rollup Calculation object.

NOTE: The Simulated Values are used in the Simulated Rollup Cost. The Standard Values are not used in the Simulated Rollup Cost. The Standard Values are the values that were used in the calculation of standard costs currently in use.
2. Navigation > Generate-Apply Simulated Rollup Costs
When the 'Apply' indicator is selected, the values in the Cost Rollup Calculation are moved to the Inventory Item Std Cost > Cumulative Simulated Tab and Single Level Simulated Tab fields.

3. Navigation > Set Standard Costs from Simulated
When this function is selected the Inventory Item Std Cost > Simulated Cost values are moved to the Inventory Item Standard Cost > Standard Cost fields.

The following details the activities when new standards are set:
-
The Cumulative Standard Tab values are moved to the Cumulative Historical Tab
-
The Single Level Standard Tab values are moved to the Single Level Historical Tab
-
The Cumulative Simulated Tab values are moved to the Cumulative Standard Tab
-
The Single Level Simulated Tab values are moved to the Single Level Standard Tab
-
Sim to Standard Roll Date set from the Cost Roll Calculation
-
Effective Date set from the Cost Rollup Calculation
-
Rollup Date set from the Cost Rollup Calculation
-
On-hand inventory is revalued at the new standard cost. The difference between the Historical Standard value (which is the standard cost prior to the new one) and the new standard value is multiplied times the on-hand quantity to calculate Inventory Cost Transactions and financial journal entries transactions.
-
Those data costing setup records (Manufacturing Department, Manufacturing Machine Master, Labor Grade, Routing Run Labor, Setup Labor, Machine Hours) having the Update option selected to Copy From Simulated have the Simulated values moved to the Standard values when new standard costs are set. When a record is set to Manual, the user must enter the value in the standard fields.
-
On the Inventory Item Standard Cost record, the Sim to Std Roll Date is populated with the date the new standard is set.
Cost Reports
Navigation > Indented BOM
The Indented BOM inquiry presents parent item BOM structure and cost. The function accesses three different cost records. The type selected determines the cost source.
NOTE: The Weighted Average Indented BOM would not be used in a Division set for Standard Cost.
The following inquiry types present costs sourced from the Inventory Item Std Cost object:
-
Single Level Standard
-
Single Level Simulated
-
Single Level Historical
-
Cumulative Standard
-
Cumulative Simulated
-
Cumulative Historical
The following inquiry types present costs sourced from the Cost Rollup Calculation object. These are the Simulated Rollup Cost resulting from the Generate Simulated Rollup Cost function being run.
The following inquiry type present costs sourced from the Inventory Item Average Cost Quantity > Last Average Cost Tab > Last Average Unit Cost, Total.
This selection presents the Weighted Average cost of each item in the BOM structure. It is not a rollup of item Weighted Average Costs. Costs are sourced from the Inventory Item Inventory Item Average Cost Quantity > Last Avg Costs Tab > Last Average Unit Cost, Total
SEE ALSO
Division Master
Inventory Item Standard Costs
Inventory Item Master
Routing Operations
Costed BOM
Rootstock Schema Builder - Standard Cost
Import: Update Inventory Item Standard Costs