Overview
A Work Order is a formal authorization for manufacturing to produce, refurbish or rework an item. The Work Order can consume material, labor and machine resources, as well as overhead charges, during the production of the item. The Work Order function provides the necessary information needed by various departments to plan, schedule and manage the manufacturing shop floor. It also provides a repository for capturing the Standard and Actual (standard cost division) or Weighted Average and Actual cost (weighted average cost division) of the Work Order.
Application
The following details how a manufacturing Work Order may be used:
-
Authorization for manufacturing to use resources in the manufacture of an item.
-
Planned and scheduled Work Orders by Work Centers.
-
Work Center Capacity Planning.
-
Production reporting of labor and quantities produced.
-
A planned standard cost of production versus an actual cost of production and the calculated variance.
-
Work in Process valuation.
-
“As-built” Work Order information. This provides a permanent record of the actual material issued to a Work Order, including non-lot and non-serial controlled items, lot controlled items, and serial controlled items.
-
Serial number usage traceability.
-
Lot number usage traceability.
Click on image to enlarge
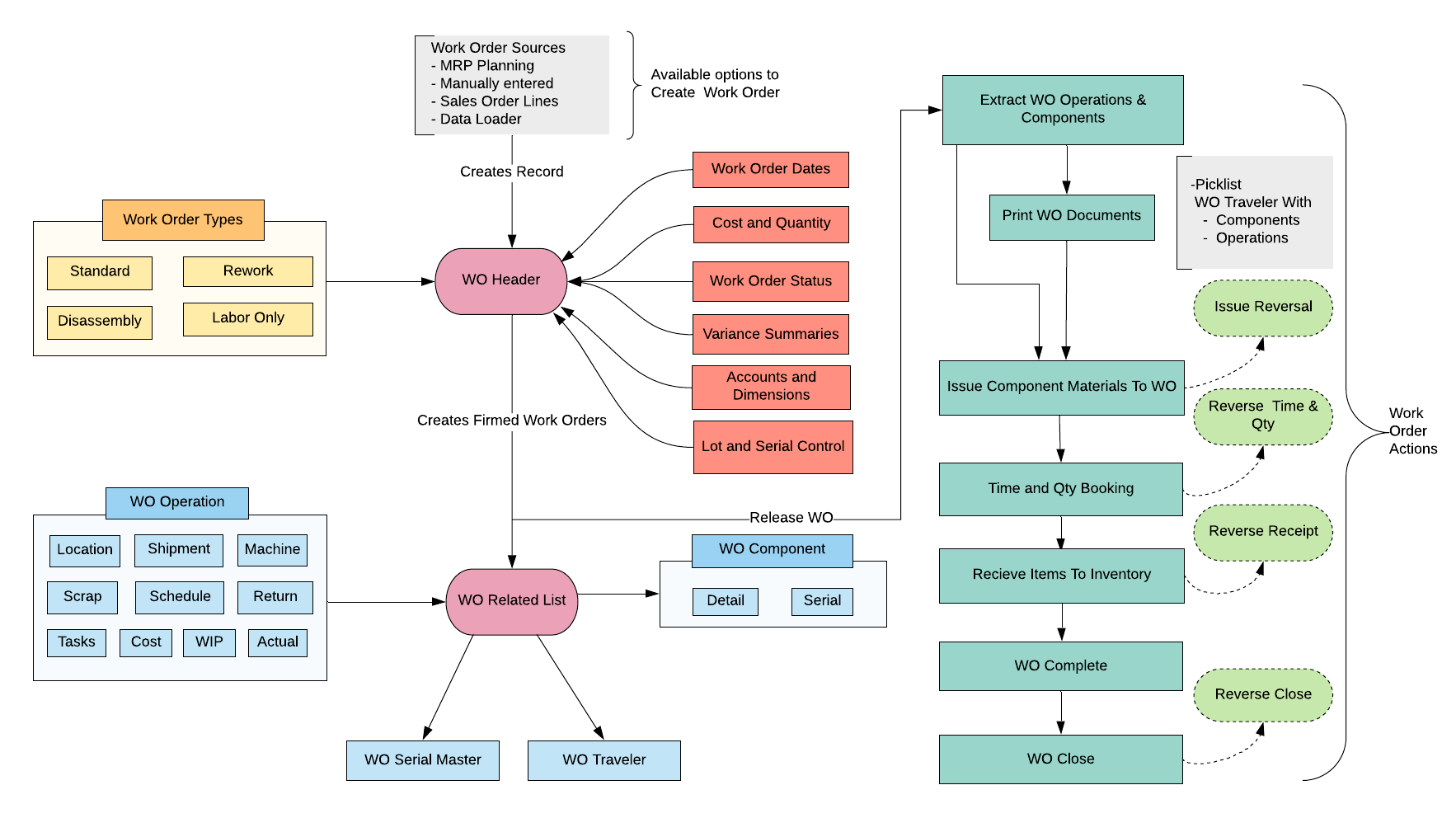
Work Orders - Table of Contents
A. Work Order Types
I. Standard Work Orders
II. Rework Work Orders
III. Disassembly Work Orders
IV. Labor Only Work Orders
B. Work Order Transactions
I. Work Order Issue
II. Work Order Issue Reversal
III. Work Order Operation Labor
IV. Work Order Receipt
a. Work Order Receipt Traveler
V. Work Order Receipt Reversal
VI. Work Order Close
VII. Work Order Close Reversal
C. Work Order Setup Requirements
D. Work Order Sources
I.Work Order Created by MRP
II. Work Order Created Manually
III. Work Order Created by Sales Order Lines
E. Work Order Header Information
I. Work Order General Information
II. Work Order Dates
III. Work Order Cost and Quantity Summaries
IV. Work Order Statuses
V. Work Order Variance Summaries
VI. Work Order Accounts and Dimensions
VII. Work Order Lot and Serial Control
F. Work Order Related Lists
I. Work Order Component
a. Work Order Component Detail
b. Work Order Component Serial
II. Work Order Operation
a.Work Order Operation Tasks
b. Work Order Operation Actual
c. Work Order Operation Cost
d. Work Order Operation Location
e. Work Order Operation Machine
f. Work Order Operation Schedule
g. Work Order Operation WIP
h.Work Order Operation Scrap
i. Work Order Outside Operation Shipment
j. Work Order Outside Operation Returned
III. Work Order Serial Master
IV. Work Order Traveler (Components / Operations)
G. Work Order Actions
I. Change Work Order Status
II. Extract Work Order Components and Routing
III. Work Order Picklist
IV. Generate Work Order Serial Numbers
V. Delete Work Order Components and Routing
VI. Back Schedule a Work Order
VII. Work Order Close, Reverse Close, and Archive
H. Work Order Component Allocations
I. Work Order Backflushing
J. Time and Quantity Booking
K. Work Order Pick List
L. User Time Entry
M. Mass Firm Work Orders
N. Consumable Components
O. Time and Quantity Booking Reversal
P. Clock-On-and-Clock-Off
Q. Consolidated Work Order Picklist