Overview
Engineering Change Orders add another level of control for companies using Revision Control to maintain bills of material and routings.
- Engineering Revision control (ER) provides a permanent record of changes to a bill of material or routing operations.
- It uses a revision identifier and a date to indicate when the revision will start.
- Inquiries and reports with selection criteria provide the capability to view and use the configuration of the items bill of material or routing to a specific item’s revision.
The decision to require Engineering Revision Control is made at the Division Level. If selected, all engineering changes within the Division will require a Revision to process.
- When RC is in control, a Revision is required to make changes to the Bill of Material or Routing.
- An Engineering Revision is defined at the level of Revision Number, Item, Start Date, and Status.
- A single Revision (Revision #) may be the controlling point for adding/deleting one or more components to/from a Bill of Material or adding/deleting one or more operations to/from a Routing.
- As long as all components and/or operations under the Revision will become Effective on the same date, multiple components and/or operations may reference the same Revision.
NOTE Refer to the Add / Delete Effectivity section of this document for examples of a single Revision controlling both the addition and deletion of components to a BOM and operations to a Routing.
The On-Hand balance considers all implemented parent level revisions to be completely interchangeable.
- The on-hand balance is not kept at the revision level, but ONLY at the item number level.
- It is possible to have within a given on-hand quantity of a Parent Item, multiple revisions of the parent assembly, each with a different underlying BOM and/or Routing.
- The planner will determine “use up” logic to consume the remaining components in inventory, if any, at the previous rev level.
When Engineering Change Orders (ECO) is active, an ECO Master is created first and then the Item Engineering Revision(ER) is identified to the ECO. The status of the ITEM’s ER is controlled by the status of the ECO. The Engineering Revision will require an Engineering Change Order as a prerequisite if Engineering Change Order Control is active.
Engineering Revision Item
Revisions are Item specific.
- A single item may go through multiple revisions.
- Other than the initial creation of the item (Rev 000000), under revision Control all future changes to the Item will require an Engineering Revision.
NOTE The initial default Rev value of 000000 cannot be changed. (All items when initially entered, whether revision control is active or not, are stamped with revision 000000).
Engineering Revision Start Date
The Start Date represents the date the Revision becomes effective.
- A Revision can Add or Delete a component; therefore, the Start Date on a Revision becomes the Add Date for components being Added and the Delete Date for components being Deleted.
- The system uses the Add / Delete Effectivity Controls to determine what is included in MRP and Cost Roll Up calculations.
Engineering Revision Status
The Engineering Revision is status controlled to represent the flow through the Engineering Revision Process.
Use the Status to identify the point in the flow for a Revision:
- Pending
- Released
- Implemented
IMPORTANT Only Engineering Revisions with a Status of Implemented are considered by MRP and Cost Roll Up. The Pending and Released status’ are used to track the movement of the revision thru the design and approval process only.
Configuration Options: Engineering Change Control – Engineering Revision – 3 Options
Bill of Materials and Routings are created and maintained under three possible division specific configuration setting scenarios:
Scenario # | Engineering Change Control | Revision Control |
1 | No | No |
2 | No | Yes |
3 | Yes | Yes |
Navigation
Division Master
The settings for control of Engineering Change Orders and Engineering Revisions are on the Division Master Record.
Fields
ECO Active: When checked, ECO is active in this division.
Eng Revision Active: When checked, (Item) Eng Revision Active in this division.
Eng Revision Format: Select the method of assigning Engineering Revision identifiers to the item
- Alpha-Numeric: User entered, user determined format.
- Numeric: Assigned by the software incremented one (1) up from the initial revision 000000
Initial Eng Revision Status: When Engineering Revision is checked (active) as a new engineering item is entered to the data base, the initial Revision Status of the Item is Pending or Released.
- Pending - User Defined, not implemented
- Released - User Defined, not implemented
- Implemented - Changes are now implemented.
Scenario #1 - Engineering Change Control – No / Revision Control - No
- Initial effective date of all BOMs and Routings are defaulted to the Start Date (Division Setting).
- Create the BOM structure or Routing. Revision #000000 is assigned.
- Delete BOM Components or Routing Operations directly via the Bill of Material or Routing Masters.
- Add / Delete effectivity of Items to the BOM or Operations to the Routing based on Add/Delete Dates (not revision effective dates since revision control is set to no).
- Can still assign status to Add/Delete (Pending/Released/Implemented), however, only the Implemented Status affects MRP and Cost Roll Up.
- A Single, current BOM or Routing is continually revised (BOM history is available via the “Indented BOM” report).
- Memo field and attached documents support revisions by documenting each change.
Scenario #2 - Engineering Change Control – No / Revision Control - Yes
- Initial Revision defaults to Rev 000000 with the description “Item Added” and with a Start Date: System Start Date (Division Master setting).
- For Bill of Material and Routing changes, create a new Revision for the parent item and assign an Effective Date. New Revisions are created using the Engineering Item Master object, Revisions tab. There you will find ‘Add Revision’.
- Additions and deletions to the Bill of Material and/or Routing are then made against the new Revision until it is implemented, at which time another Revision will be used for additional changes.
- First Revision after Rev 000000 uses Add /Delete effectivity dates on Revisions to add/delete components or operations and to control the BOM Component quantity per parent and Routing Operation quantity (time) per parent.
- Add /Delete effectivity dates for component and operation changes are defaulted to the Start Date of the Revision.
- Item inventory continues to be managed by Item # only (Not by Revision).
Scenario #3 - Engineering Change Control – Yes / Revision Control - Yes
- Initial Revision defaults to Rev 000000 with the description “Item Added” and with a Start Date: System Start Date (Division Master).
NOTE An ECO can be assigned to REV 000000 but it is not required.
- For Bill of Material and Routing changes, create a new Engineering Change Order and related Revision for the parent item and assign a Start Date.
- ECO’s can be tied to an item (component) as well as parent items.
- Additions and deletions to the Bill of Material and Routing are then made against the new Revision.
- First Revision after Rev 000000 uses Add /Delete effectivity dates on Revisions to add/delete components or operations and to control the BOM Component quantity per parent and Routing Operation quantity (time) per parent.
- Add /Delete effectivity dates for component and operation changes are defaulted to the Start Dates of the Revision.
- Item inventory continues to be managed by Item # only (Not by Revision).
- ECO’s can be status Pending/Released/Implemented. Revision changes tied to an ECO are not active unless the ECO is status “Implemented”
- The ECO “Date” and Revision Start Date are independent; the new Revision Start Date cannot be prior to the ECO implemented “Date”
Application
Engineering Revisions and Engineering Change Orders are used when there is a need to locate an item’s configuration (bill of material) or manufacturing operations (routing operations) at a specific point in time.
EXAMPLE How did we manufacture that item this time last year? What components did we use to make the parent item six months ago?
Terminology
Engineering Change Control: Engineering Change Control is a functional tool to control Item Engineering Revisions.
- A single Engineering Change Control Master can control the status of one or multiple individual Item Engineering Revisions.
Engineering Revision: The Engineering Revision Control effects both Bill of Materials and Routings.
- Items and Routings are stamped with a Revision number and controlled by start and end dates.
- A single Revision (Revision #) may be the controlling point in adding/deleting one or more components to/from a Bill of Material or adding/deleting one or more operations to/from a Routing.
NOTE When Engineering Revision is active Bills of Material and Routings are controlled by Revision.
Engineering Revision Start Date: This represents the date the Revision becomes effective.
- A Revision can Add or Delete a component, therefore the Start Date on a Revision becomes the Add Date for components being Added and becomes the Delete Date for components being Deleted.
- The system uses the Add / Delete Effectivity Controls to determine what is included in MRP and Cost Roll Up calculations.
Division: Engineering Change Order and Engineering Revision functionality are controlled at the Division level.
Effectivity – Add and Delete Control
- Add and Delete Effectivity controls exist at the item level within the Bill of Material and at the operation level within Routings.
- These controls determine which Revision is being used and when the Revision becomes effective.
- Implemented Revisions only are considered for MRP and Cost Roll Up.
NOTE Add Effectivity defines the Revision for inclusion to the BOM or Routing configuration on the Revision Start Date. Delete Effectivity defines the Revision as exclusion from the BOM or Routing configuration on the Revision Start Date.
- Under Revision Control, a component added to an existing Bill of Material, or an operation added to an existing routing, would need a Revision using Add Effectivity to add the item or operation, and a second Revision using Delete Effectivity to exclude the item or operation.
- The Revision Start Date becomes the Effective Date of the Revision.
- Use the Revision Start Date and the Add and Delete Effectivity Controls to manage the add and delete of components over the life span of the item.
- A Revision can Add or Delete a component or operation; therefore the Start Date on a Revision becomes the Add Date for revisions being Phased In and becomes the Delete Date for revisions being Phased Out.
IMPORTANT Without Revision control, components are added directly to the Bill of Material and do not require a revision to do so. However, this method does not allow the user to ‘see’ how an item was manufactured or what components were used at any time in the past.
Add Effectivity
- Revision Number
- Status
- Revision Start Date is the Add Effective Date
Delete Effectivity
- Revision Number
- Status
- Revision Start Date is the Delete Effective Date
Example: Revision Control BOM
- Add Parent Item A-100 to Engineering Item Master.
- Rev000000 as Initial Revision Automatically Assigned.
- Under Rev000000 configure the original Bill of Material.
- Implement Rev000000.
Use a Revision to change the configuration of parent A-100.
- Define Revision (Rev01) to Parent A-100.
- Use Rev01 to Add component C on the Rev01 Start Date.
- The Rev01 Start Date becomes the Add Effective Date reflecting the first day the component is in effect (implemented).
Define Revision (Rev02) to Parent A-100.
- Use Rev02 to Delete component C on the Rev02 Start Date.
- The Rev02 Start Date becomes the Delete Effective Date for component C reflecting the last day the component is in effect.
Use Rev02 to Add component D on the Rev02 Start Date.
- The Rev02 Start Date becomes the Add Effective Date for component D reflecting the first day the component is in effect.
In this example Component C was added under Rev01 with an Effective Date of 05/01/2011. Rev02 was then used to stop Component C and add Component D. Rev02 is used for both the deletion of Component C and the addition of Component D.
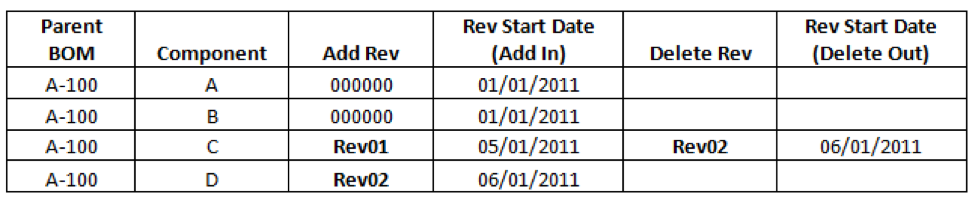
Example: Revision Control Routing Example
- Add a Routing for item A-100 to the Routing Master.
- Use a Revision to change the Routing for item A-100.
- Define Revision (Rev01) to Parent A-100.
- Use Rev01 to Add a new operation to the routing on the Rev01 Start Date.
- The Rev01 Start Date becomes the Add Effective Date reflecting the first day the new operation is in effect.
- Define Revision (Rev02) to Parent A-100.
- Use Rev02 to Delete an existing operation on the Rev02 Start Date.
- The Rev02 Start Date becomes the Delete Effective Date reflecting the last day the operation is in effect.
- Use Rev02 to Add a new operation on the Rev02 Start Date.
- The Rev02 Start Date becomes the Add Effective Date for the new operation reflecting the first day the component is in effect.
In this example a Visual Inspection Operation was added under Rev01 with an Effective Date of 05/01/2011. Rev02 was then used to stop the Visual Inspection and start the Machine Inspection. Rev02 is used for both the deletion of Operation Visual Inspection and the addition of Operation Machine Inspection.
Example: Various ECO and ER configurations
Create a Change to a Bill of Material or Routing with both ECO Control and Revision Control Active
- Create a new ECO
- Use ECO Detail Tab to create the related Revision.
- Manage ECO and Revision.
The Revision Status cannot be changed to Implemented until the ECO status is changed to Implemented. If the ECO Status is changed to Implemented, then all Revisions attached to the ECO also become ‘Implemented’. The Effective Date of the ECO will set the Effective Date of the related Revision.
NOTE Only Revisions with a Status of Implemented will affect MRP and Cost.
- Use the Revision to modify the Bill of Material or Routing based on Revision Start Date and Add Effectivity Control.
Create a Change to a Bill of Material or Routing with ECO Control Not Active and Revision Control Active
- On the Engineering Item Master use the Revision Tab to create a new revision.
- Manage Revision - The Revision Status must be ‘Implemented’ for the Revision to be included in the MRP or Cost Roll Up.
- Use the Revision to modify the Bill of Material or Routing based on Revision Start Date and Add / Delete Effectivity Control. Make the Bill of Material or Routing changes first, and then implement the Revision.
Create a Change to a Bill of Material or routing with No ECO Control and No Revision Control
- Navigate directly to Bill of Material or Routing and add/delete a component or operation. Use the Add / Delete Effectivity control to determine when the component or operation is in effect.
SEE ALSO