Overview
This function contains a record for each component item in each Bill of Material.
-
Each Bill of Material is linked to a parent item number.
-
The Bill of Material contains one or more required components to build the parent item.
-
Each Bill of Material component item record contains information used to determine the specific requirements (quantity and date) for MRP Planning, Work Order costing, and Work Order execution.
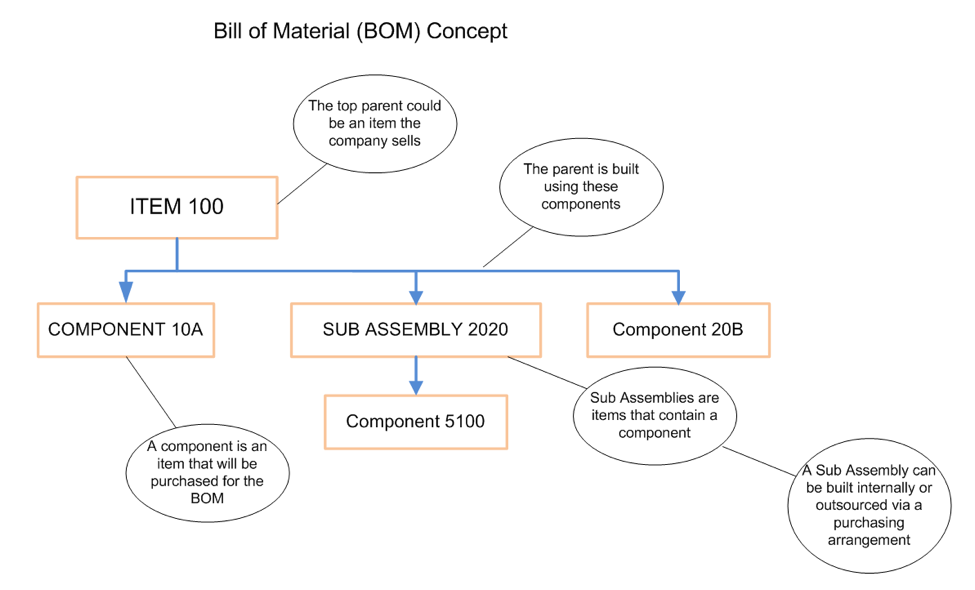
A Parent Item may have a single or multiple levels in the Bill of Material.
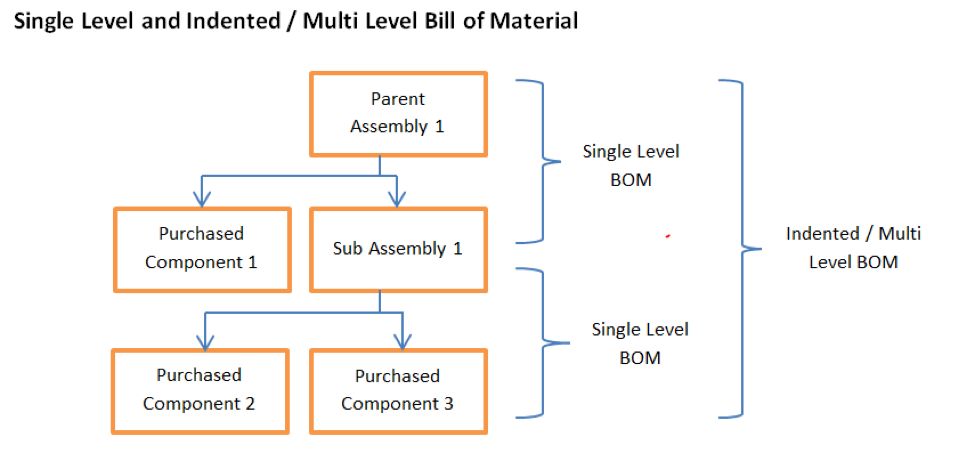
Application
The Bill of Material Master is used to:
-
Add a new component item to a parent item.
-
View a component-parent record.
-
Edit a component-parent record.
-
Delete a component parent record
NOTE The deletion capability is only available within the BOM Master when Engineering Revision (ER) is inactive. If ER and/or ECO are active, changes to the BOM are made through those functions.
BOM Maintenance applies the industry standard Single-Level Bill of Material concept to achieve an Indented / Multiple-Level Bill of Material.
The Bill of Material structure is used for engineering configuration, Material Planning, Work Order and Purchase Order pick lists, and product costing.
NOTE If a component with Eng Type of Phantom or Reference is added to a BOM, there will be no demands generated for either as a component on a Work Order or Subcontract PO. Reference items added will print on an associated Picklist for the Parent after all standard components but will not be picked as part of the process since there is no demand. Phantom items added as a component will generate demands against the Parent Item for each of the components of the Phantom but will not create a demand for the Phantom itself.
Terminology
BOM Overrides: Overrides for the component in the BOM.
MRP Overrides: Overrides specific to this parent-component record.
-
Used in MRP planning.
-
Overrides may be applied to the scrap factor, Setup Quantity, Fixed Quantity, and Phantom designation.
Multi-Level BOM: A bill of material showing all items needed to manufacture the parent. A multi-level BOM shows all subassembly components and single-level BOMs.
Phase In: The ER and ECO (if active) control the phase-in of a component item in a BOM.
Phase Out: The ER and ECO (if active) control the phase-out of a component item in a BOM.
Reference Designators: Additional drawing information specific to the parent-component relationship on the drawing.
EXAMPLE A drawing call out number.
Single Level BOM: Consists of the parent item and component items and/or subassemblies, including the quantity required to make the parent.
NOTE Components required for the subassemblies are not included.
Navigation
Engineering BOM Master
Processing
Entering and Maintaining a BOM Master Record
1. List View
The Engineering BOM (Bill of Material) Master starts with a List View displaying all records within the BOM file.
2. Select the Record to Edit or click the New BOM Master button.
Fields
Parent Item (Required): The BOM parent item number must be a valid engineering part number.
Component Item (Required): The component item number being added to the Parent BOM.
Add Revision (Required): Select when ER is active.
Quantity Per (Required): Quantity of the component in the BOM to build 1 parent item.
Line Number (Optional): Line Number
Click on the ‘New BOM Master’ to enter a new bill-of-material record.
NOTE Using this function, you must add components one at a time, saving each one as an individual BOM record.
TIP For efficiency, the BOM Mass Add function should be used when adding multiple components.
Enter each field following field help and drop-down options.
NOTE Some fields, such as ‘Division’, may have a prerequisite entry.
IMPORTANT If Revision Control and/or Engineering Change Control are inactive, the BOM master record can be maintained here. If those options are active, the record cannot be maintained here; an Engineering Revision or ECO must be created.
Phase In and Phase Out Tab
Phase In and Phase Out controls exist at the item level within the Bill of Material.
MRP Overrides Tab
MRP Overrides allow the user to control the quantity required of each component beyond the standard quantity per function.
Fields
Scrap Factor: This field indicates how much component scrap is produced when the parent item is manufactured or subcontracted.
-
The system first calculates the component’s required standard quantity by adding the component quantity and the Setup Qty (if used) together.
-
It then uses the scrap factor to determine how much of that total quantity will be lost as scrap, determining the total component quantity required to meet the actual demand.
Setup Quantity: This is the amount of the component that will be lost when setting up the production machine. It is a static number added to the calculated BOM quantity required to determine the total quantity required before the scrap factor is considered.
Fixed Quantity: If checked, this field indicates the BOM quantity-per to be fixed, as opposed to a BOM quantity multiplied by the work order required quantity.
Phantom Override: This override allows items classified as Phantoms to be viewed as standard items for this particular BOM.
Ref Designator Tab
Reference Designators (Ref Designators) are generally used to define the location on a drawing or part where components are located.
NOTE Separate each reference designator with a comma, semi-colon, or space.
BOM Overrides Tab
BOM overrides allow the user to define certain changes to the standard BOM. These changes will be used by MRP and pick-list creation until they are removed.
NOTE The ‘Add Override’ button is only available here when Engineering Change Control and Revision Control are not used in this division.
Fields
Quantity Per: The override quantity for this component on this BOM only.
Scrap Factor: The override scrap factor (expressed as a decimal quantity) to be used for this component.
Work Center: The work center where this component will be consumed.
Lead Time Offset: The number of days after the release of the Work Order that this component will be needed. This number is used by MRP to plan the required available date for purchases and/or manufacturing.
Setup Qty: The override setup quantity for this component.
Process No.: The process to be used as an override when manufacturing this parent item.
Save the Record when all override entries have been done.
SEE ALSO
Engineering Item Master
Engineering BOM Query Edit
Work Orders