Introduction
The purpose of this article is to present a summary overview of topics relevant to cost in Rootstock. Topics have an entry "Note See Also - Article Name". This references an article or articles that provide detailed information.
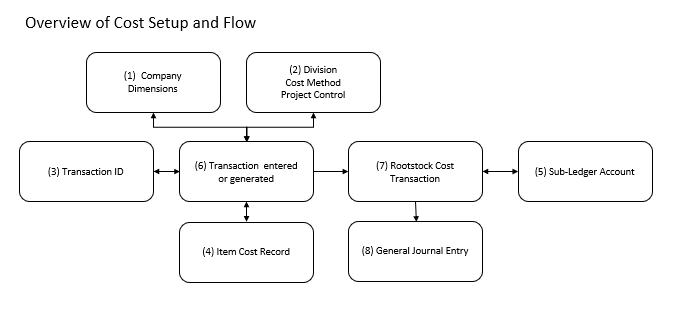
Summary of the setup
-
Company Master record and user-defined Dimensions are entered.
-
Division Master record, the cost method is selected. Project Control, as required, is made active.
-
A predefined set of Rootstock predefined Transaction IDs.
-
Item Cost Record.
-
Sub-Ledger Accounts (Division).
Summary of Cost Flow
-
A transaction is entered or generated.
-
The Transaction ID is assigned.
-
The Item Cost is assigned.
-
The Dimension is assigned.
-
The Project ID is assigned.
-
A Rootstock Cost Transaction is created.
-
A General Journal Entry is generated from the Rootstock Cost Transaction.
NOTE The numbering in the diagram refers to the numbering of the following topics.
Setup for Cost
(1) Company Master - Dimensions
Dimensions are user-defined identifiers, such as classes or categories. Dimensions are assigned to Rootstock Cost Transactions and General Ledger transactions. Dimensions support the segregation of costs into user-defined classes or categories to satisfy the reporting requirements.
Note: See Also -
Company Master
(2) Division Master - Rootstock Cost Methods and Projects
-
Rootstock provides two cost methods. Standard Cost and Weighted Average Cost.
-
When the Standard Cost method is selected, item standard costs are set periodically and do not change until the next periodic setting. The variance calculation is the difference between the Item’s standard cost and the Purchase or Manufacturing cost. The cost of an item in any transaction is the Standard Cost of the item.
-
With Weighted Cost, each receipt transaction results in a recalculation of the Weighted Average Cost of the transacted item. The format of the calculation is: ((The current value in inventory + the value of the receipt) / (current on-hand quantity in inventory + receipt quantity)).
-
When the Division cost method is Weighted Average, an available option for user-selected purchased items is FIFO (First-In-First-Out) cost. When the Division Cost Method is Standard Cost, the FIFO option is unavailable.
-
Project Control function is active in a Division.
-
Project Master records can be manually entered or auto-generated by the software. In a Division with Project Control active, all transactions require a Project identifier to be assigned.
-
Job Code and Project Charge Code functions provide enhanced functionality to Project Control. The Job Code capability gives additional visibility to the actual cost of work performed. The Project Charge Code is used to classify Project-related transactions. Also, there may be Project costs in addition to Inventory Items. These costs are identified by the name Other Direct Charges (ODC). An example is purchased Engineering Services.
-
General Ledger (GL) transactions are generated from the Rootstock Cost Transaction. The project identifier field is in both the Rootstock Cost Transaction and the General Journal Entry.
(3) Transaction ID (Identifier)
Rootstock has predefined Transaction IDs. The IDs identify the type of transaction, such as Purchase Order Receipts, Work Order Receipts, Sales Order Fulfillment, Inventory Adjustments, and other types of transactions. When a transaction is entered or generated, Rootstock assigns a Transaction ID.
Note: See Also -
Rootstock Cost Transaction ID and Sub ID Listing
(4) Item Cost Record, Cost Elements – Standard Cost and Weighted Average
The values in the Item Cost record is assigned to all transactions. The transaction with the cost is the basis for the Cost of Goods Sold reporting, Inventory Valuation, and Cost Analysis activities.
Whether the Division’s selected cost method is Weighted Average or Standard, each item has ten cost elements and a total cost. The cost element used by each item will vary with the Item Inventory Source Code. For example, a Purchased Item will not have a Labor cost element value, whereas a Manufactured Item will have a Labor Cost element value. When a Division uses the Standard Cost Method, the costs are periodically set standard costs. When the Division is a Weighted Average Cost method, the costs are Weighted Average cost calculation.
The available ten cost elements are:
Material: Cost of Purchased Material
-
In a Weighted Average Cost Division, this is the weighted average material cost of the Item.
-
In a Standard Cost Division, this is the standard cost of the material.
Labor: The cost of Labor to manufacture an item.
-
In a Weighted Average Cost Division, the Item’s Labor Cost is calculated by multiplying the actual hours reported with the employee’s hourly labor rate.
-
In a Standard Cost Division, the cost of labor is calculated by multiplying the operation’s Standard Labor Hours with the labor grade rate assigned to the operation.
Labor Overhead: This is calculated by multiplying the Manufacturing Department Labor Overhead Rate by the Labor Cost.
Fringe Overhead: This is calculated by multiplying the Manufacturing Department Fringe Rate times the Labor Cost.
Freight: Freight as an inventory cost of acquisition.
Other Landed Cost: Other costs, such as duty and brokers fees, as an inventory cost of acquisition.
Machine Overhead: Calculated using the Machine Hours and Machine Hourly Rate.
Subcontract Material: Cost of material supplied by or to the Vendor.
Outside Labor: The cost of the Vendor’s labor on a Work Order operation.
Total: Total cost of the ten cost elements.
Values in the various cost elements vary with the Inventory Source Code. Here are some examples.
-
The Inventory Source of Purchased is assigned to items acquired from a Vendor using a Purchase Order. The typical cost elements for these items are Material, Material Overhead, and possibly Freight and Other Landed Costs.
-
The Inventory Source of Subcontract Purchased is assigned to items purchased from a Vendor, and the Purchasing Division may supply some or all of the parts the Vendor requires. The typical cost elements for these items are Material, Material overhead, Subcontract Material, and possibly Freight and Other Landed Costs.
-
The Inventory Source of Manufactured is assigned to items manufactured on a Work Order. The cost of the Manufactured Item is a total of the cost of all the component materials (Purchased, Subcontract Purchased, and Manufactured) issued to the Work Order and the cost of Labor, Labor Overhead, Fringe Overhead, and Machine Overhead used to manufacture the item.
(5) Sub Ledger Accounts
The Rootstock Sub-Ledger functionality provides for the definition of a detailed manufacturing Sub-Ledger account structure independent of but mapped to the Financial General Ledger Accounts. A separate set of Sub-Ledger Accounts is created for each Division. Each Rootstock Sub-Ledger Account is mapped to a Financial General Ledger Account. The mapping between the Sub-Ledger and the General Ledger Accounts can be One-to-One or Many-to-One.
Note: See Also -
Sub-Ledger Accounts TerminologyNote: See Also -
Sub-Ledger AccountsNote: See Also -
Cost Element Account Detail
Transactions and Cost
(6) Transactions Entered or Generated
The source of transactions may be a user entry or generated by Rootstock. A transaction starts the recording of an item’s acquisition, used in manufacturing, adjusting of inventory, or fulfilling an order. Each transaction contains an Item Number, a reference to the activity, and it may or may not reference an Order Number.
(7) Rootstock Cost Transaction (AKA: Inventory Cost Transaction)
When the entered or generated transaction is processed, a Rootstock Cost Transaction record is created. It is a permanent, non-auditable record of the details of each transaction. Examples of the information contained are the Transaction ID, Project ID, Dimensions, Item Number, Cost, and Sub-Ledger Debit and Credit accounts.
Note: See Also -
Inventory Cost Transactions
(8) General Journal Entry
As the entered or generated transactions are processed, from the information in the Rootstock Cost Transaction, a General Ledger Journal Entry is created and posted.
SEE ALSO